BUILDING STATISTICS
Part I

Building Facts
Building Name (Fictitious)
Location
Occupancy Type
Size
Number of Floors
Caribbean Hotel
Kingston, Jamaica
Hospitality (Hotel/Resort)
155,000 square feet
6
Project Team
*Click on name to go to website
Owner
Architect
Landscape Architect
Design Consultant
MEP and FP Engineer
Structural Engineer
Civil Engineer
Confidential
Bruce Howard & Assoc.
Stanley D. Lindsey
Hue Lyew Chin Eng.
Architecture
Design and Functional Components:
This project was designed to capture the renewed vitality of the area in which it resides. The building will contain approximately 220 rooms, a large conference center, a full service restaurant, car showrooms, event space, retail, a pool, and more.
The most demanding requirements of applicable codes and standards (identified year or latest edition where not indicated) of following will apply:
-
Jamaica National Building Codes (JNBC)
-
JNBC Volume 2, Energy Efficiency Building Code
-
International Building Code (IBC) with local amendments, 2009
-
International Mechanical Code (IMC) with local amendments, 2009
-
International Plumbing Code (IPC) with local amendments, 2009
-
International Energy Conservation Code with local amendments, 2009
-
ASHRAE Standard 90.1 - 2007
-
ASHRAE Standard 62.1 - 2007
-
ADA Standards for Accessible Design
-
National Fire Codes (NFPA)
-
SMACNA Standards and Guidelines
Construction Details
Dates of Construction
Approximate Cost
Project Delivery Method
January 2017-Winter 2019
$50 Million
Design - Bid - Build

Building Enclosure
The “L”-shaped building has two main parts to it. The shorter half will contain a ballroom on the ground floor with retail space above it. This portions façade will consist mostly of thermally insulated concrete. The larger half of the “L”-shape will be on the south side of the property where the 220 hotel rooms reside. Glass is the main exterior finish for the majority of the surface area here.
Facade:
The majority of the building’s exterior walls is comprised of a curtain wall system. This particular system is made up of hurricane and impact resistant materials (aluminum and glass mostly) with Low-E insulating glass. This glass with contribute to keeping the building loads as low as possible for a curtain wall system by reflecting infrared energy also known as heat.
Roof:
The roofing system contains a fully adhered membrane, lightweight insulating concrete, eps rigid insulation board, and a continuous vapor barrier built up above the poured in place concrete roof slab. The slope is 1/4” per foot slope to drains located throughout the roof surface.


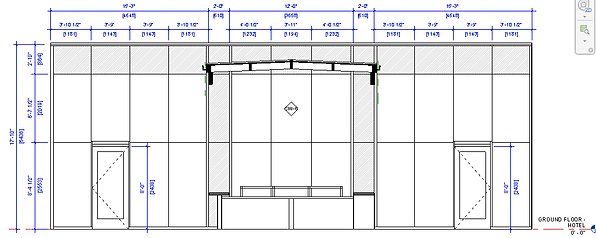
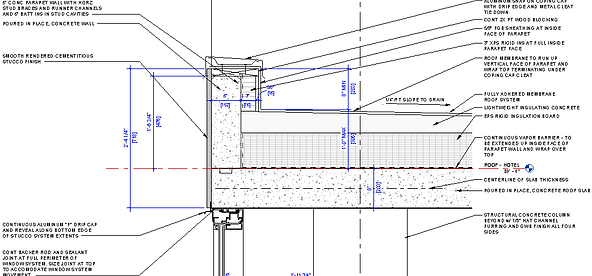
Sustainability
All building energy codes were met while designing this building, although it is still in construction so further data has yet to be analyzed. This building did not complete any sustainable or LEED status’s during design, however the equipment and materials were chosen based on both cost and energy efficiency.
Part II
Primary Engineering Systems
Construction:
Construction for The Caribbean Hotel began in January 2017 and will end in Winter 2019, lasting approximately 24 months. The contract type utilized for this project is the Design-Bid-Build method. The cost of this 155,000 square foot building is around $50 Million, and there will be 6 above grade floors and no floors below grade when construction is finished.
Electrical:
The main power for this site comes into the service transformer “T-UHA” that is 415Y/240V, 3 Phase, 4 Wire, 50 Hz secondary. There is also a 2500 Amp Generator on site, “C-GENHA” 415Y/230V, 3 Phase, 4 wire, 50 Hz (1440/1800KW/kVA) that serves the building. The transformer goes to switchboard “C-N00MSBHA”, then to Automatic Transfer Switches, then to Distribution Panels. The transfer switches are for Equipment served as: standby (100kAIC), normal (100kAIC), life safety (65kAIC), and emergency (65kAIC). The generator serves the fire protection control panel and fire pump, then Distribution panel “C-G00MSBHA”, then to the same automatic transfer switches aforementioned. The power from the switches then goes to distribution panels,
then utilizes stepdown transformers to smaller panels. This building utilizes a High Voltage system of 415Y/240 Volts, 3 Phase, 4 Wire; and a Low voltage 240/120, Volts 1 Phase, 3 Wire. The grand total front of house lighting zone load for 730 total fixtures is 19611.802 VA.
Lighting:
This building’s lighting design complies with the power density codes and illuminance criteria in accordance with the Illuminating Engineering Society Lighting Handbook, 10th Edition and ASHRAE 90.1 2013 Building Code. All lighting fixtures selected are high efficiency LED’s. Daylighting was maximized through the large curtain walls, especially in the lobby where parallel facades allowed the brightness of the light penetration to be the main source of lighting during the day. Almost all indoor lights have a Correlated Color Temperature of 3000K, or “warm white”. All lights utilize a voltage of 120V, with the exception of certain lights that are 240V and usually outside. The circulation spaces within this building are to remain on at all times with no substantial dimming protocols,
but are zoned by type and have wall switches to turn them off or on if need be. Exterior fixtures are controlled by a timer which is preset to the hours of operation. The ballroom lighting is equipped with color changing fixtures and is integrated with AV systems to allow for a dynamic space. The fitness center is equipped with daylighting controls and sensors to maintain a constant illuminance.
Mechanical:
The Caribbean Hotel is approximately 155,000 square feet of building with multiple different types of spaces in it which require different types of cooling (also, not much heating is required because of the Caribbean location’s climate). There will be a central plant that will be comprised of two (2) 350 ton air cooled chillers. These chillers will be located on the roof of the ground floor offices and will serve a total of 13 Air Handling Units, 2 DOAS units, and 1 Makeup Air Unit serving the building providing approximately 28,000 CFM of supply air to the system.
This hotel will contain 220 guestrooms which will be conditioned with horizontal chilled water fan coil units with electric heating coils, and will be provided ventilation air through vertical duct risers at either end of the corridors distributed through horizontal ductwork. Guestroom corridors will also be ventilated and temperature controlled by two DOAS units from the roof that will also provide the ventilated air to the guestrooms and their corridors. The front of house, amenities, and back of house spaces on grade will be air conditioned using chilled water air handling units with individual zones (example of this zoning shown below in Figure 1) served by VAV boxes with electric reheat coils. Other amenities, office areas, and back of house spaces will be served by chilled water fan coil units with electric reheat coils, and outdoor ventilation air from DOAS units will be provided to occupancies that are served by fan coil units.
Structural:
The structural system of this building is comprised of rectangular mat foundations and footings 3 feet below grade. The gravity system for the ballroom is comprised of 5” thick one way concrete slabs with reinforced concrete beams of various sizes and configurations, and rectangular reinforced concrete columns on the first floor. The ballroom roof is comprised of W12x40 steel beams in the N-S direction with six trusses at various spacing in the E-W direction supporting the beams. In the south east corner of the ballroom there are W12x 26 steel beams supporting various solar panels. The main gravity system of the hotel consists of 8” reinforced concrete two way slabs with Rectangular reinforced concrete columns and 8” reinforced concrete interior and exterior load bearing walls. For the lateral resisting system 8” reinforced concrete shear walls are integrated within the staircases and elevator shafts.
Additional & Support Engineering Systems
Fire Protection:
The fire protection system complies with NFPA #13, 14, 20, and all applicable state and local codes, and all sprinklers will have corrosive-resistant coating, and sprinklers shall cover the entire area of all structural members. Design density split into 3 hazard categories (light, ordinary 1, ordinary 2) with proper sprinkler head spacing (225,130,130) and hose allowance (100,250,250) based off of design demand.
This site has a free standing fire department connection with check valve in the vertical rise located within 100 feet from fire hydrant, near the north west corner of the fitness center. There is also a 60,000 water storage tank below the slab for the hydraulic piping system.
The Fire Pump Room contains a 125 HP Electric Fire Pump rated for 1000 GPM at 155 PSI with a fire pump controller with automatic transfer switch; 3 HP electric jockey pump rated for 10 GPM at 165 PSI with a wall mounted controller; an 8” pump test line with flow meter to discharge back to cistern; and a 36” manway access with a ladder.


Transportation:
There are 2 elevators in this building with stairwells located next to either of them. A main corridor runs between the two rows of guestrooms in the hotel tower, and the lobby is the main point of circulation on the first floor of the entire building with corridors branching off into the areas with other rooms.
Special Systems:
There are 14 Domestic Hot Water Solar Panels located on the ballroom facility roof and facing due south contribute to the Solar Heated Water Loop Piping system for Guestroom and Kitchen Hot Water Supply supplemented by two Instant Gas Fired Domestic Water Heaters.
